Crosscut Sled for Large Panels
Steve Fikar's panel sled is guided by a single runner in one miter slot attached to a torsion-box base to keep the sled light.
Synopsis: Crosscutting large sheet goods accurately can be a challenge, so most woodworkers turn to a crosscut sled. The typical design tends to be very heavy when built to hold a large sheet, so Steve Fikar designed this sled, guided by a single runner in one miter slot, that runs along one side of the blade. Torsion-box construction keeps the base from getting too heavy. The single runner is made from a steel bar for durability.
I cut out large plywood parts pretty regularly for a variety of woodworking projects, including cabinets for the house and shop. Ripping these big pieces on the tablesaw is easy enough, but crosscutting them accurately is a challenge. A tablesaw crosscut sled will do the trick, of course, but if you stick to the usual design, a large-capacity sled tends to be very heavy. So I decided to start with a clean slate and engineer something unique.

My solution is an extralarge sled that runs along one side of the blade—instead of straddling it— guided by a single runner in one of the miter slots. To add size and capacity to the sled without adding weight, I borrowed a common engineering solution—torsion-box construction—to create a 3⁄8-in.-thick base that is very lightweight yet remarkably stiff and strong.
As they are on all crosscut sleds, the fence and base on this sled are trimmed by the blade, creating zero-clearance support for chip-free cuts and easier alignment. An advantage of a one-sided sled is that only one fence is needed, attached at the front edge.
Steel runner ensures accuracy
The main disadvantage of a one-sided sled, especially a large one with heavy cargo, is the single runner that guides it. If it were made from wood, it would tend to wear and get sloppy over time. So I used a steel bar for this sled—“cold-rolled” at the factory to precise dimensions—which will deliver a lifetime of accurate cuts.
Most tablesaw miter-gauge slots are milled to fit a straight bar exactly 3/4 in. wide by 3/8 in. thick. You can buy a steel bar with these precise dimensions from a variety of online retailers, in a 3-ft. length that’s perfect for this project.

Just to be sure, though, measure your miter slots with a dial caliper and read the specs carefully on the bar you’re considering. The one I found at McMaster-Carr is perfect for my saw, with a tolerance range from a few thousandths undersize up to 0.750 in. on the nose. If there’s any doubt, err toward a slightly undersize bar and dimple it to fit, as shown above.
Start by building the torsion-box base
The top and bottom layers of the base are full sheets of hardboard, while the middle layer is a grid of 1-in.-wide strips with open spaces between, making the base somewhat hollow yet extremely stiff.
From Fine Woodworking #292
To view the entire article, please click the View PDF button below.
![]() |
Build a Tablesaw Sled for MitersThis precision jig eliminates gaps and headaches. |
![]() |
Tablesaw sleds for joinery |
![]() |
3 Sleds for Better Crosscuts |
Fine Woodworking Recommended Products
Veritas Precision Square
Ridgid EB4424 Oscillating Spindle/Belt Sander
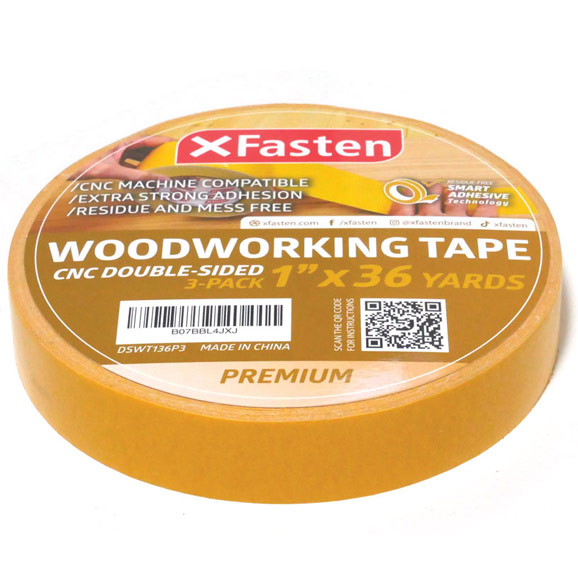
Double Sided Tape
Comments
Seems like overkill. What are you cutting the panels for? If you can rip one side, then putting that side against the fence for another rip cut will give you a square corner. For cutting panels for a door, the panel will fit into slots and should have some room for movement that can be centered with a dab of silicon glue in the slot.
I have a similar design made out of 1/2" ply with a wood runner. Hot wax runner with paraffin, align back cleat with square, screw down from top to fix runner, standard stuff.
I just used mine to trim the ends of a 24 x 48 hickory coffee table for a bread board end. Even had a clamp just like the lead picture. Will it matter it the cut is off by 0.010" over 24"? Nope, everything came out fine.
Everyone has their own needs for being able to crosscut large panels. I like the precision that this sled gives me as I do not depend on square corners from the factory. The accurate cross cuts pay off for me with all the cabinets I have made over the years. I can make crosscuts up to 3' wide if necessary so it has more capacity than I will ever need. I no longer have to get out my skill saw to make a large square crosscut anymore. I am glad you have a similar design and hope you are happy with it too.
I use a fair amount of 5' X 5' multi-ply and can't rely on the factory for square corners or clean edges. I've been trying to square two sides with a track saw but this looks like a much quicker and easier way to do it.
I would like to find some jaw covers for my mechanic vise like his. They look like they might be a hard rubber or plastic. I find myself working on things I don't want to beat up my woodworking vise with but don't want the teeth on my mechanic vise marring it up. I made some wooden covers but they get splintered up fairly quickly.
mlcswoodworking has something similar to the vise jaw covers,
https://www.mlcswoodworking.com/shopsite_sc/store/html/smarthtml/pages/magnetic_aluminum_jaws.html?zoom_highlight=vise
Wow Thanks 3fingerjack those jaw covers are just what I've been looking for. Got to get a couple of them.
Just curious. Do the flat "torsion" strips really add rigidity? Don't torsion designs gain their strength from the lateral rigidity of a thicker "web"? Would gluing up a sandwich of three full sheets achieve the same or greater strength? Thanks.
To answer your questions –
Do the flat "torsion" strips really add rigidity?
Yes.
Don't torsion designs gain their strength from the lateral rigidity of a thicker "web"?
Yes, the thicker the web, the greater the stiffness. Since I wanted to keep the sled thin (3/8”) the web pieces had to also be very thin at 1/8”. Even with the thin web, the sled is extremely stiff, much more than plywood of the same thickness.
Would gluing up a sandwich of three full sheets achieve the same or greater strength?
In reference to ‘strength’, I assume you mean ‘stiffness’. Three full sheets would perhaps add a small amount of extra stiffness, but it would be minimal. It would, however, increase the weight of the sled. The whole idea of a torsion box is to add lots of stiffness with minimal weight.
I wish you the best!
A possible improvement: I have used transfer punches to mark the wooden piece to be drilled through the threaded bar holes in order to avoid damaging the threads with a drill bit and to get an exact center. Love your project.
Log in or create an account to post a comment.
Sign up Log in