Building with MDF
Medium-density fiberboard offers both quality and stability. Here, William Duckworth provides some tips and tricks for working with it.At the risk of inviting the scorn of some purists, I’m here to make a bold declaration: For painted cabinetry, there is no better and more appropriate product to use than medium-density fiberboard (MDF). And virtually any species available as the face veneer of hardwood plywood is also available with an MDF core.
No material is perfect, of course, but in the case of MDF, the pros far outweigh the cons. MDF is inexpensive and extremely stable, and it’s manufactured in consistent thicknesses (unlike most plywood). In some ways, using MDF is more environmentally friendly than using solid lumber because there is an inexhaustible, renewable supply of the raw material MDF is made from—a supply that will be available for generations to come. On the downside, though, sheets of MDF are heavy, and the dust that is kicked up when you cut and rout the material can be, at best, an irritating nuisance; at worst, it can be a health hazard if your exposure is extreme.
What is MDF?
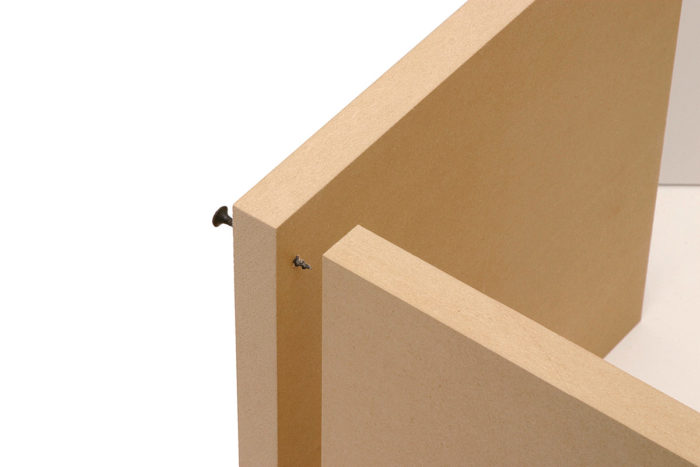
Until conducting research to prepare for this article, I knew little about MDF besides that it is a wood composite. I got my hands on industry documents that describe the contents and manufacture of MDF in terms that sound almost like language you’d expect to hear in medical school—cellulosic fibers, tracheids, pendistors, and defribrators. Put in layman’s terms, most MDF can be defined as panel products made from wood that has been pulverized into tiny fibers, heated, mixed with glue, pressed to a consistent thickness, dried, and cut to size.
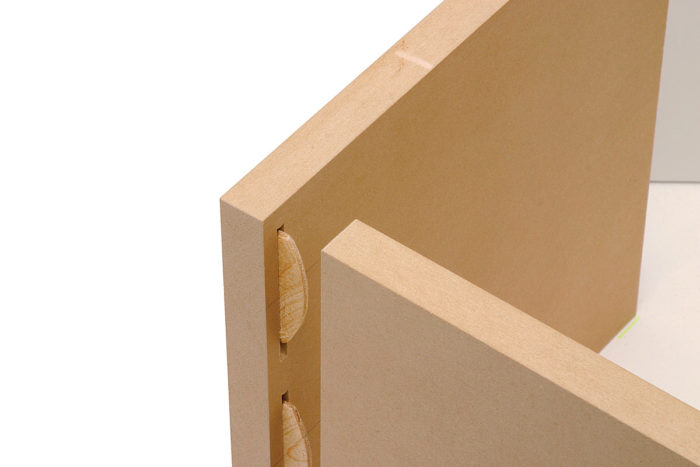
MDF cores are not as strong as most lumber and plywood, but when joining together pieces of MDF, you can use just about any joint that you would use with plywood: butt joints with screws, biscuits, splines, fully rabbeted edges, and rabbeted tongues in dadoed grooves. You also can miter the edges if you want an invisible joint in a pre-veneered panel, but be sure to use plenty of glue on the mitered edges because they’re so porous.
MDF has its limits
Deciding whether to use simple or complex joinery in cabinets is always a judgment call. Most casework is fairly simple, and it rarely has to be engineered to carry heavy loads, so butt joints with screws are sufficient. But when cabinets will be subjected to stress (a heavy television, a stone countertop) or abuse (young children who like to slam doors), don’t skimp on the glue and screws.
You must drill properly sized pilot holes whenever you fasten a screw into an MDF edge; otherwise, it will split readily. For casework, I like to use a rabbeted tongue in a dadoed groove. This joint is not as important for the added glue surface and strength it may provide as it is for the assistance it renders when you’re assembling large cabinets. It makes the job a lot easier, especially when you’re working alone.
The industry differentiates between three density grades of MDF: low (weighs less than 40 lb. per cu. ft.), standard (40 lb. to 50 lb. per cu. ft.), and high (more than 50 lb. per cu. ft). And like any product manufactured competitively, there is a huge variety in kind and quality, even within the standard-density grade that makes up most of the MDF made and sold.
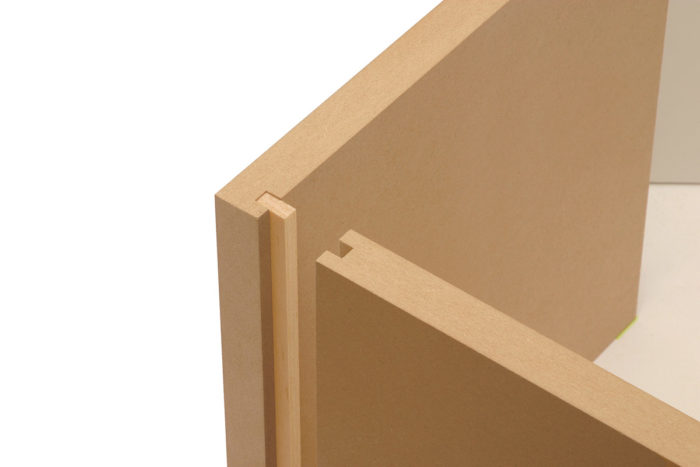

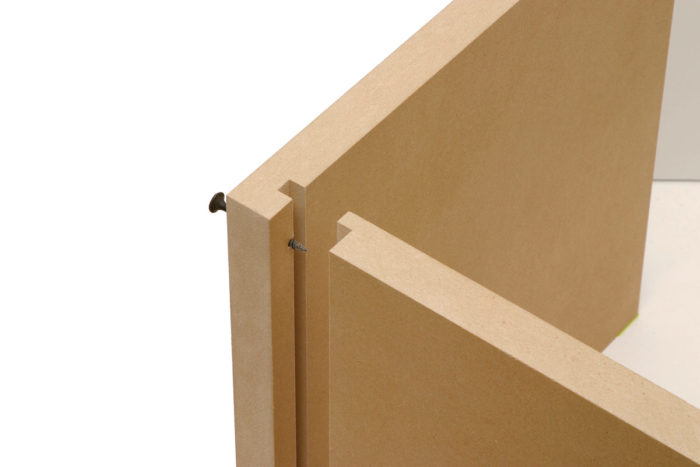
Sustainable options
Urea formaldehyde (UF) resins have been the primary adhesive for the composite-panel industry since its inception in the years shortly after World War II. UF resins lend strength and stability to the finished panels, at a reasonable cost, but they offer only limited moisture resistance.
They also emit small amounts of formaldehyde, which can irritate eyes and respiratory systems and possibly cause more severe health problems in people with extreme sensitivities to it. If you or a family member fits that category, you can buy a formaldehyde-free panel. The Medite Corporation makes Medex and Medite II—moisture-resistant and interior-grade MDF panels that emit extremely low levels of formaldehyde.
Melamine-fortified UF resins and phenol-formaldehyde (PF) resins are glues sometimes used to enhance the water resistance of the final product. Methyl-diisocyanate glues are used in panels made from agrifibers for the same reason. There is no such thing as waterproof MDF, but Medex—which was developed for nonstructural, high-moisture applications such as countertops, bathroom cabinets, baseboards, and painted windowsills—is rated as highly water resistant.
The Buyers and Specifiers Guide, published by the Composite Panel Association, lists a couple of plants in Canada that make an exterior-grade MDF using spruce and pine as the raw material.
For surfaces that will be painted, MDF has no equal
For painted cabinets, furniture, wall paneling, and some moldings, MDF is a great choice. Surface faces come from the factory sanded to 150-grit or better, essentially paint-ready. I scuff-sand the surface quickly with 120-grit or 150-grit sandpaper to remove dirt and grime and to provide for better adhesion of the primer coat.
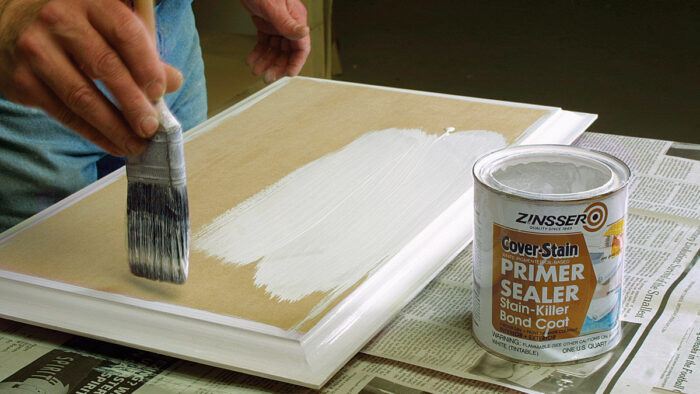
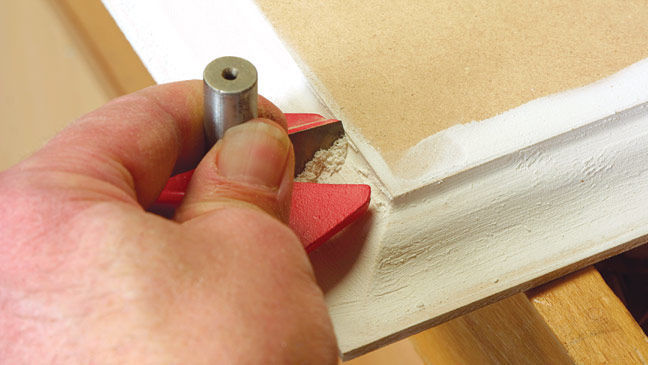
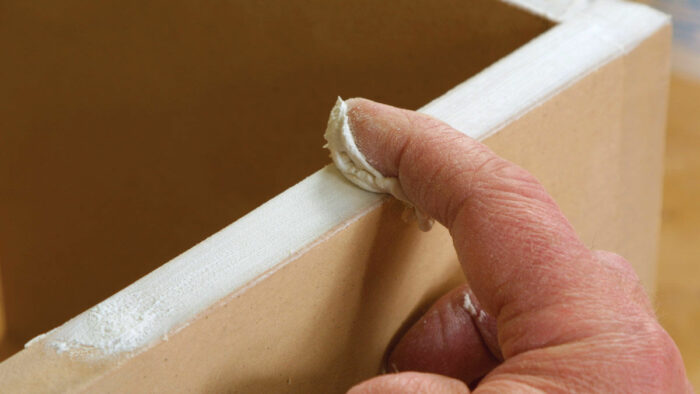
Solvent-based primers (oil-, alcohol-, or lacquer-based) are a must. Never use a water-based product for the initial finish coat. The wood fibers will swell too much when they absorb the water, and you’ll get what is, in effect, raised grain on the surface that will not sand out. After the surface has been sealed with something else, though, a water-based paint will not affect the MDF adversely. I use latex paint over properly sealed wall paneling and trim molding, but for painted furniture or cabinets, I prefer the finish quality of oil- or lacquer-based paint applied with a spray gun.
I use drywall compound to fill the edges, whether they are cut squarely or shaped with a router bit, and I apply the compound liberally with a finger or the palm of my hand. Unlike spackle or conventional wood putties, drywall compound has a soupy texture, so it’s a little sloppy going on. But after it dries, it sands off easily.
For edges shaped with a router, you can use the same router bit as a scraper to remove the excess globs of compound before touching up the edges with 220-grit, silicon-carbide sandpaper.
A Quick Tongue-And-Groove Joint on the Tablesaw
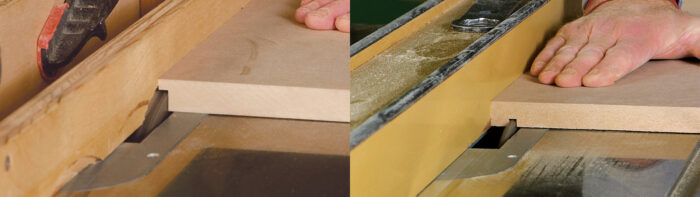
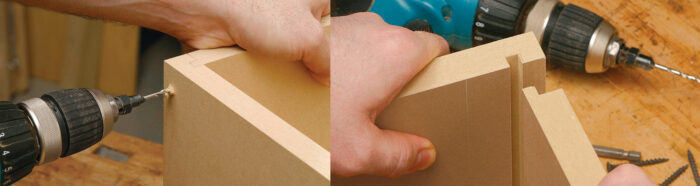
William Duckworth is a woodworker in Woodbury, Conn., and a former contributing editor to Fine Woodworking.
This article was originally featured in our new stand issue “Built-Ins” in 2006. Some information is derived from A Woodworker’s Guide to Medium-Density Fiberboard.
![]() |
Tips for Painting MDF |
![]() |
Video: Preparing to Veneer MDF |
![]() |
Does MDF Belong in Fine Furniture? |
Fine Woodworking Recommended Products
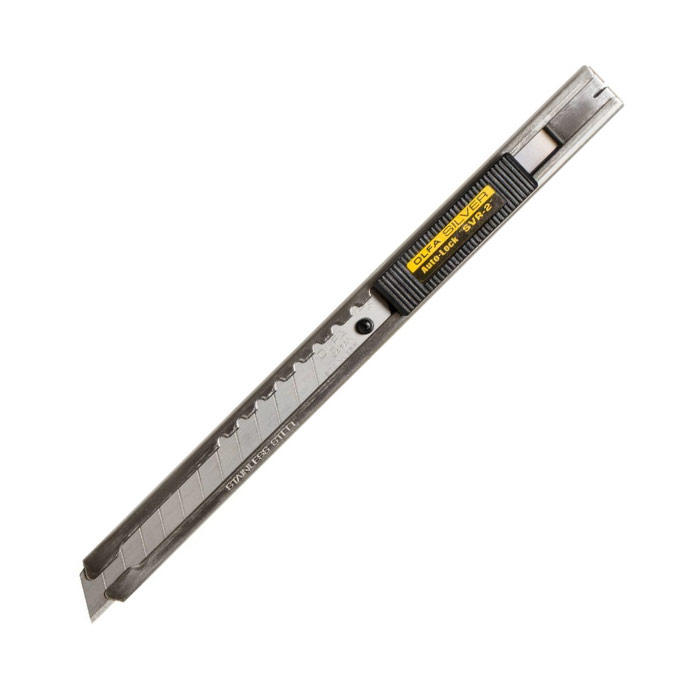
Olfa Knife
Ridgid EB4424 Oscillating Spindle/Belt Sander
Starrett 4" Double Square
Comments
Is it possible to laminate the mdf panels after the screw butt joints so that the screw wont be visible ?
I find it hard to believe that you are talking about building furniture with MDF and you still want to call yourself "Fine" Woodworking magazine. What's next? OSB?
jrwatt: Architectural grade MDF and OSB are the panel of choice when doing high-end veneer work and making cabinetry boxes because, unlike solid wood and plywood, they are dead flat and they don't move. These are not construction grade panels. They are architectural grade. All professional cabinet shops use them and you should too. In my time as a professional cabinet maker, I always used pre-finished, veneered OSB to make my boxes. I prefered OSB because the joinery is better than with MDF and I was always veneering rather than painted. But MDF is available at your local box store while architectural OSB is not. MDF and it is the material of choice if you're going to paint. You can even get it primed.
Is the spline material also MDF? Or can it be something like 1/4" plywood?
What's more readily available and affordable, a massive clamping system like this one or a vacuum system?
Log in or create an account to post a comment.
Sign up Log in