Curly Cherry Highboy, Part One
Combine hand and machine techniques to produce an American furniture classicSynopsis: The first of three articles on how to build a beautiful curly cherry highboy. This Early American reproduction has a bonnet top, a dramatic gooseneck molding, brasses, carved fans and finials and cabriole legs. Randall O’Donnell explains how to build the base, from selecting the stock to shaping the legs, mortising the leg posts, and preparing the stock for the carcase. He explains how to cut out the front rails, sides, and back, and he explains how to make the interior framing members. He assembles the base in three stages before attaching the knee blocks or fitting the tenon pins. A detailed project plan and multiple photos illustrate the process.
When I watch a sawyer cut open a hardwood log that has highly figured wood inside, it’s like stumbling across a buried treasure. Wood like that is a gift of nature, and it deserves the best showcase I can provide.
Most of the pieces that I make are reproductions of Early American furniture, and for showing off unusually beautiful lumber, there’s nothing quite like a high chest of drawers. Unlike a tabletop, a highboy can be appreciated from a distance and the character of the wood really becomes three-dimensional. Add a bonnet top with a dramatic gooseneck molding, brasses and carved fans and finials—all dancing on cabriole legs—and the result is a piece of furniture with real presence.
I’ve examined a number of original highboys. Only a few stand out as true masterpieces, but many include wonderful details that provide a rich palette for the period furnituremaker. This piece is my interpretation of a Massachusetts style from about 1750. The blocked apron, finials, arch cutouts and shells are based on designs from Boston in that era.
The highboy exercises just about every skill of the traditional cabinetmaker: turning, sculpting, mortise-and-tenon joinery, dovetailing, carving and (gasp!) even driving nails where appropriate. Colonial cabinetmakers usually had apprentices handle routine tasks. As an independent craftsman, my apprentices are machines that prepare stock quickly so that I can devote my time to the critical hand skills that set this piece apart from factory-made furniture. Fine carving, hand-cut dovetails and handplaned surfaces remove any trace of the machines that did the grunt work before me. Economic reality has taught me that even though I can replicate a period piece of furniture, I can’t slavishly follow every method of the Colonial makers.
Building this highboy is well within the abilities of the serious amateur cabinetmaker. Although it may appear daunting, much of the work amounts to executing just a few traditional joinery techniques over and over. With so many pieces to cut and assemble, organization is as important as technique.
Select stock carefully
All the curly cherry flat stock needs to finish out at in. thick, so I usually start with roughsawn, 1 in. stock. The gooseneck molding and lower finials are made from curly cherry stock, and I use sound straight-grained stock for the legs and the top finials.
From Fine Woodworking #117
For the full article, download the PDF below:
Fine Woodworking Recommended Products
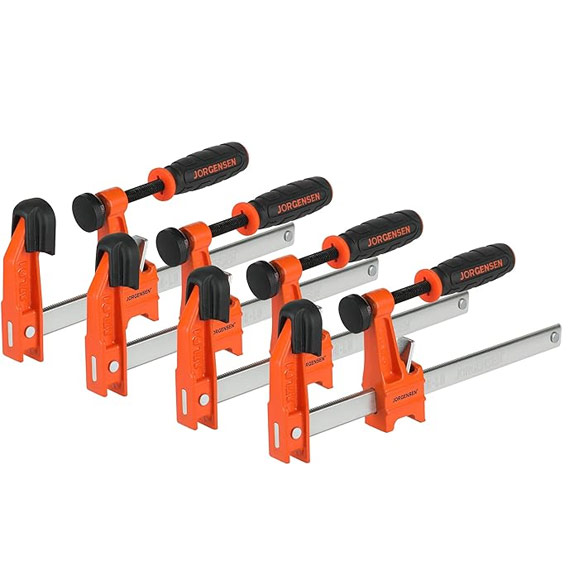
Jorgensen 6 inch Bar Clamp Set, 4 Pack
Starrett 12-in. combination square
Bessey EKH Trigger Clamps
Log in or create an account to post a comment.
Sign up Log in