Here’s how I make backs for wall cabinets: I take a piece of plywood, usually 1/4 in. thick, apply edge bandings, and then glue on some shop sawn veneers. I end up with a back that’s 3/8 in. thick. Why do I make them that way? Well, I tend to make wall cabinets that are no more than 6 in. deep. I just don’t like the way deeper cabinets poke out into the room. But when the cabinet is so shallow, most traditional methods for hanging the cabinet become a problem. A French cleat for a cabinet this size, for example, would need to be 1/4 in. – 3/8 in. thick. And you can’t have it proud of the back, because then you have some unsightly gaps with light sneaking through between the wall and cabinet. And if you inset the cleat, you lose an equal amount of interior space on an already shallow cabinet. Add it’s thickness to the thickness of the back and you’re talking about 5/8 in. – 3/4 in. of depth lost. No good.
What I needed was a strong back that didn’t take up too much space. Plywood is strong. So I started to explore how I could use it to make an attractive and strong back. I have done enough shopsawn veneer that I immediately thought of gluing some shopmade veneers to a plywood core. That took care of the attractiveness. I knew that a back made that way would be strong, but also about 3/16 in. thick. So, I decided to make the rabbet for the back just 1/4 in. thick and leave the back 1/8 in. proud of the cabinet. When put against the wall, you get a nice shadow line between the wall and cabinet.
Of course, making a back this way means making shopsawn veneer, which can be tough if you don’t have a drum sander. Veneers, which should be no more than 1/8 in. thick, are really too thin to go through a planer. So how do you clean up both sides without a drum sander? Handplaning can work on short pieces, but the pieces needed for a back are too long and tend to bow up as you plane them.
My solution? Make a back from slip-matched veneers. Here’s what I do.
1. Prepare the plywood core: cut it to size and glue on edge banding.
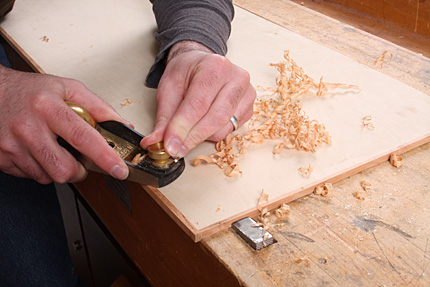
2. Joint one face and one edge of a thick board.3. Cut the first piece of veneer.
4. Re-joint the face.
5. Cut the second piece of veneer.
6. Repeat until you as many pieces as you need.
7. Edge glue the individual pieces to create a wide sheet (How I do that.). Here’s where the slip matching comes into play: All of the jointed faces end up on the same side of the sheet.
|
|
8. Glue the sheet down to the plywood, rough side up.
9. After gluing both the front and back sheets to the plywood, you can clean up the surfaces with a handplane or planer (I’ve done both) as you might a thick piece of solid wood.
So, slip matching gets around the problem of surfacing thin stock, because you can glue it to the core and then surface the veneer.
As for attaching the cabinet to the wall, I use two anchors and hide them behind drawers. For a small cabinet, I even have the anchors at the bottom of the cabinet, where I usually put drawers. They’re so light and don’t get weighed down, so there’s no danger of the top pulling away from the wall.
Comments
Mat using plywood? All joking aside, good tip.
what method do you use to glue the veneer to the plywood? vacuum or cauls? I've been wanting to give this a try with some expensive wood and have been stalling out here. My project entails some larger panels and using 5/8" thick plywood to arrive at a 3/4" thick panel.
mangledandrus,
I use a vacuum press for all of my veneering. I have the Vac Pro Plus kit vacuum press from veneersupplies.com. It works great. If you have a big enough compressor, you can use a bag up to 4 ft. by 9 ft.
Matt
Do you have any problems with the panel warping since the veneer is only glued to one side? Or, is this not a problem since you are adding another "ply" to the plywood?
JoeHorn,
Good question, and I should have been more clear about this. I am actually veneering both sides of the plywood. Definitely do both, or it will warp. Sorry for not saying that in the blog.
Perfect timing Matt - I'm planning a build that needs some veneer work. Could you give your opinion on MDF v Ply as the core? I've been reading up on this and the pros and cons from people seem pretty evenly matched. I'm thinking if veneering the table top of the dining table I'm building and haven't got the funds to allow for any mistakes.
Also which glue/s would you recommend?
cheers,
Jon
NikonD80,
As long as there is adequate support under the top, then it doesn't matter which one you use. However, I would probably opt for a high quality baltic birch plywood. Plywood holds screws much better than MDF and I assume you're going to screw the top to the base in some fashion. Also, high quality plywood won't have any voids in it.
Matt
Log in or create an account to post a comment.
Sign up Log in