Tambour doors now and then
Polish furniture maker Tom Bensari takes a look at the evolution of the tambour door, from its roots in 18th century France to contemporary furniture collections.The history of tambour-door furniture dates back to France in the 18th century and begins at the court of Louis XV, where a royal ébénist was given the task of creating a bureau du roi—a desk for the king at which he could work freely and store documents, books, and writing utensils. From the beginning, the function of the tambour doors was purely practical: to easily and conveniently conceal the ruler’s workspace.

This revolutionary enclosure quickly moved from writing desks to chests and other types of storage furniture as well as to closets and architectural applications. Then the tambour-door cylinder desk gained popularity in the United States, where it was widely adopted as office furniture because of the safety of storing documents in it. It is to the American market that we owe the terms rolltop desk or American desk.
The tambour moves to private spaces

The decorative character and functionality of tambour doors were also recognized by representatives of European modernism in the 1920s. Tambour doors used to obscure the interiors of cabinets or alcoves were perfectly in line with the “spatial austerity” (German: raumersparnis) they postulated. The architect and designer Le Corbusier appreciated the functional and aesthetic qualities of movable wooden obscurants, presenting a piece of furniture with tambour doors at the 1925 World Exhibition in Paris.
With the development of modernism in design and architecture, tambour doors ceased to be clearly associated with office furniture and entered more and more boldly into public and private spaces. Tambour doors with vertical slats became particularly popular, as their arrangement introduced rhythm and dynamism into interiors. Tambour doors tempted designers with huge possibilities for modification—in the width of the slats, the profile, and the species of wood used.
Trademark tambours
Wooden tambour doors with perfectly preserved wood grain have become my trademark. The inspiration for my first collection of furniture with tambour doors, “Chameleon,” was the modernist facade of the Kameleon department store in Wroclaw, Poland. I worked with artist and designer Roland Grabkowski, who interpreted the building’s characteristic horizontal divisions and rounded bay windows with sculptural sensitivity to translate them into beautiful and functional pieces of furniture. Wooden tambour doors with vertical slats perfectly complemented the design, giving it visual lightness while serving their practical purpose of covering the bar and drawers for small items.
Visual continuity is important

When making tambours, there is a cluster of considerations to take into account before deciding on the technical aspects of their manufacture. You need to decide if you want tambour doors with clear divisions; should the slats be made of solid wood or veneered; should they ride on wooden or metal rails, or perhaps slide in a groove, as was the case in the 18th and 19th centuries.
Another question to address is how to ensure the visual continuity of veneered tambour doors. In the case of tambour doors veneered with linear grain direction, this is not a problem, but it worsens if you want to use a more decorative veneer such as crotch or burl.
When cutting veneer for tambours, a kerf greater than 0.4 mm will cause the wood grain to show an unpleasant, not continuous effect. This effect will be greater the more slanted the grain on the veneer and the thicker the kerf left by the tool. Increasing the distance between individual slats can soften the effect a bit, but it still will be more or less visible. In my work, I use either a knife or a hand saw, giving me an almost invisible kerf and a perfect visual effect.
![]() |
![]() |
The technical side of the tambour
If you are building tambour doors from solid wood, you must begin with an analysis of wood’s behavior. In the case of longer tambour doors, the expansion and contraction of the wood will affect the fabric to which the slats are glued. In the past, hide glue was used with the addition of glycerin, making the glue more flexible. Today the spectrum of possibilities is larger, and I use Titebond Ultimate 3.
Consider the substrate
It is worth considering plywood as a veneer substrate, as MDF or other sheet goods may not be strong enough
for this application. If you choose to veneer on plywood, you should use a counter veneer on the back. This will eliminate stress and provide balance to the roller blind.
Sturdy fabric is important
The fabric for lining the tambour doors should not be stretchy. I use natural linen, which provides durability and maintains the integrity of the roller blind. When choosing the fabric for the roller blind, it is worth checking the direction of the threads. Plan the tambour doors so that the line of the fabric runs crosswise to the slats. I use natural linen with a weight of at least 240 g/square meter. To glue the fabric, I use Titebond Original; it is a little more flexible.
—Tom Bensari builds furniture and teaches traditional carpentry in Wroclaw, Poland.
To view the entire article, please click the View PDF button below.
Fine Woodworking Recommended Products
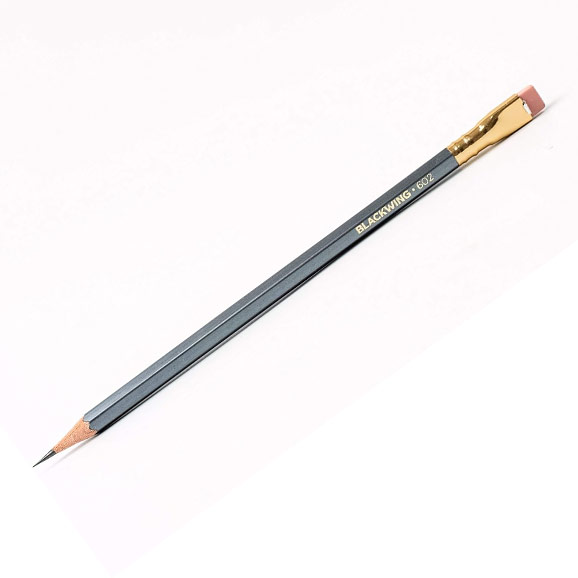
Blackwing Pencils
Sketchup Class
Compass
Log in or create an account to post a comment.
Sign up Log in