Q:
I recently acquired a 5-hp, 1-1/4-in. spindle shaper. I intend to make a set of raised panels on it using a very large cutting head, and I am concerned about safety. Is it acceptable to mount the cutter so that the head is above the work and lowered down to make the cut?
Steve Glazier, Winston-Salem, NC
A:
It is much safer in general to run the cutter below the table because of the reduced exposure. However, if the finished stock must be a critical thickness, such as a panel edge to fit snugly into the groove in a frame, mounting the cutter above the table is more efficient. By setting the correct distance between the cutter and the table, you guarantee that the thickness of all the panels will be uniform. Unlike router bits, shaper cutters can be installed face up or face down and the rotation can be reversed. Panel cutters are designed to run face down with a typical right-to-left feed (or face up, under the panel, from left to right with the rotation reversed).
For above-the-panel shaping, start by mounting a stock Lexan guard with a center bearing over the cutter. Do not mount a plywood disk or a piece of Lexan or Plexiglas with a hole cut into it directly on top of the cutter. Doing so would turn what was intended to be a guard into a spinning weapon.
![]() |
Don’t shape without the proper guard. The bearing on this Lexan guard keeps it from spinning with the cutter. A spinning guard can cut or burn you seriously. |
I also use a shopmade hold-down that presses the panel flat against the table. There should be enough downward pressure to keep the panel from lifting, but not enough to make it hard to push the panel through. Remember that with the cutter mounted above, catastrophic consequences can occur if the panel should lift up from the table.
![]() |
Shopmade hold-down is crucial. Make the hold-down from plywood by drilling and cutting alternating spring cuts. Clamp the hold-down with a spacer block between it and the fence to clear the shaper bit and avoid tilting the workpiece. Click to enlarge. |
For a large, raised-panel cutter, I run the shaper somewhere around 4,000 rpm. I ride my panels on an auxiliary table that has a small clearance around the cutter to prevent the panel from dipping into the table opening.
Back up the stock with a push board. Start by shaping an end-grain side and go around the piece counterclockwise. That way, your final pass will be along the face grain, reducing the likelihood of blowing out the corner details.
![]() |
Safety first. With the hold-down against the fence and a piece of scrap serving as a push block, your hands stay far from the cutter. It is safer and you’ll get a cleaner cut by making several shallow passes. |
One final safety rule: As with all power-tool operations, if you don’t feel comfortable doing this task, don’t do it. Period.
Drawing: John Tetreault
Fine Woodworking Recommended Products
Rockler Dust Right 650 CFM
Ridgid EB4424 Oscillating Spindle/Belt Sander
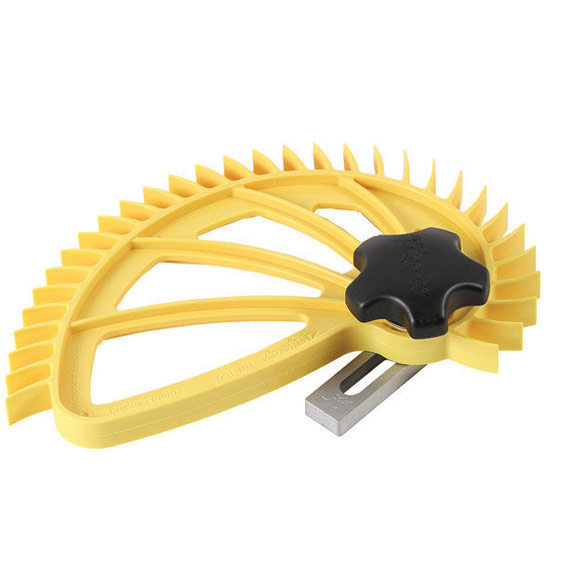
Hedgehog featherboards
Log in or create an account to post a comment.
Sign up Log in