Resawing on the Bandsaw
For predictable results, use a high fence and a very tight bladeSynopsis: Ronald Volbrecht makes guitars from extremely rare hardwoods. When it’s time to resaw these irreplaceable planks, he doesn’t want anything to go wrong. Over the years, he learned how to adjust his bandsaw for consistent results with little waste. He can get 3/32-in.-thick guitar backs from resawn boards that are only 1/8 in. thick. In this article, he tells how to upgrade your motor and pulleys, how to choose a good blade and keep it tight, how to set the speed, and how to tighten adjusting screws and set the fence. He feeds the stock in slowly and supports it. A side article by Anatole Burkin of Fine Woodworking explains how two tool manufacturing representatives advise maintaining and using a bandsaw.
I buy quilted maple for the backs and the sides of the guitars I make from a friend who is a lumber grader. Each year he inspects more than a million board feet of lumber, and if I’m lucky, he will find three good 2½-in.-thick planks. Some of the hardwoods and old-growth spruce I use are no less rare.
When it comes time to resaw these irreplaceable planks, I don’t want anything to go wrong. Over the years, I’ve learned to adjust my bandsaw for consistent resawing with very little waste. I can get finished, 3/32-in.-thick guitar backs from resawn boards that are only 1/8in. thick.
I do all my resawing on a 21-year-oid Delta 14-in. bandsaw. It has a 6-in. column extension, which allows me to resaw planks that are up to 12¼in. wide. The boards I resaw are usually 8 in. to 10 in. wide. I use a ½-in. blade with 3 teeth per inch (tpi).
Other than replacing the motor, I have not made any modifications to the saw, and I have no magic tricks. But there is more to getting good results than just running a board through the saw.
I tune my blade, set the guides close to the blade and then make sure that the blade is good and tight. I use wrenches to lock down all the adjustment points on the saw so that they can’t vibrate loose. Then I feed the plank slowly against a high fence (see the photo on the facing page), judging the feed rate by the sound of the blade.
A heavy-duty motor and new pulleys
When I bought the saw, it had a ½-hp, 1,750-rpm motor, but I soon replaced it with a ¾-hp, 3,450-rpm motor. Because the bigger motor turned faster, I had to change the pulleys to keep the blade running near the factory speed of 3,000 feet per minute (fpm).
I used the formula given in the box above to determine the right combination of pulleys. I kept the 2-in. pulley that came with the motor. That pulley and an 8½-in. pulley on the saw would have given me the right blade speed, but the big pulley wasn’t in stock locally. I tried a 12-in. pulley, but the blade ran too slowly (about 2,100 fpm). Each time the weld went through the guides, the saw lurched. I ended up with an 11-in. pulley, which turns the blade at about 2,300 fpm. That’s just about right for the work I do.
From Fine Woodworking #122
For the full article, download the PDF below:
Fine Woodworking Recommended Products
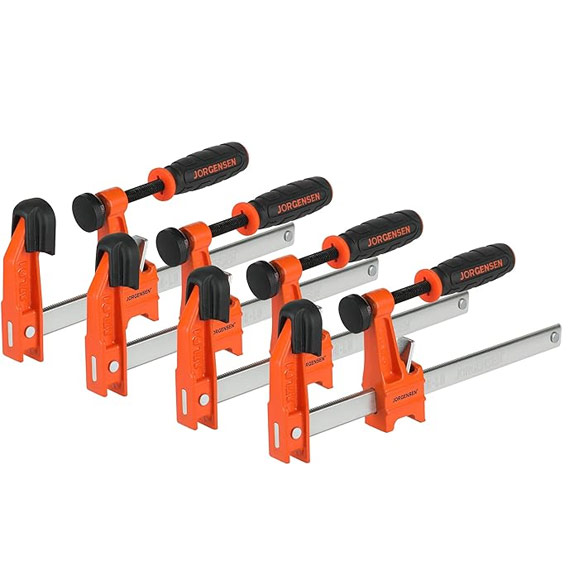
Jorgensen 6 inch Bar Clamp Set, 4 Pack
Festool Rotex FEQ-Plus Random Orbital Sander
Stanley Powerlock 16-ft. tape measure
Log in or create an account to post a comment.
Sign up Log in