Synopsis: Using a torsion box, you can make high-quality veneered furniture, curved panels, benches, shelves, and more, writes Ian J. Kirby, without a lot of weight yet ensuring strength and stability. He talks about more of the torsion box’s virtues, and he explains how to make a sample panel, how to join the core grid, how to handle surfaces and edges, joinery, wall mounting, and curved panels. Photos and illustrations leave little doubt in this course in torsion-box construction.
Suppose you wanted to make a low bench about 18 in. wide and 4 ft. long, cantilevered out from a wall with no supporting structure underneath. In solid wood, you’d have to use a plank 2 in. thick or thicker, so this simple bench would consume at least 12 bd. ft. of wood, and it would weigh 40 lb. or more. Then you’d have the devil’s own tussle figuring out how to hang it on the wall.
If you used a torsion box, you could make the same bench from less than 3 bd. ft. of wood and 12 sq. ft. of 1/4-in. plywood. It could be any thickness you wanted, it would weigh about 10 lb., and it would be child’s play to cantilever it from the wall. The torsion box is especially suitable for building high-quality veneered furniture, because it’s both lighter and more stable than a conventional lumbercore structure. It’s probably the simplest way to make a curved panel, and the ease with which the designer can manipulate the thickness dimension is truly liberating. At the same time, the torsion-box system is well within the technical reach of the amateur craftsman and the small professional shop.
As used in furnituremaking, the torsion box is two thin skins of plywood glued to a core grid of thin wooden strips. The resulting structure has strength not present in either the skin or the core alone—it’s strong the same way an airplane wing is strong. In particular, a torsion box has tremendous resistance to twisting and bending forces. This is because the structure’s geometry converts any applied force into shearing stress on the glue lines between skin and core grid. And a sound glue line is strongest in its resistance to shearing stress.
The concept behind the torsion box isn’t new. Engineers use it for box beams as well as for airplane wings, and the same concept makes possible the structural steel I-beam. The system described here was developed in Europe during the 1960s for the manufacture of large wardrobes and other case goods for storage. The traditional way of making a wardrobe is to join four pieces of wood at the corners, firmly attach a back, and hang doors on the front. Although the back contributes a great deal to rigidity, the front corner of a 6-ft. wardrobe can still be lifted several inches off the floor with the other three legs remaining on the ground. Any unevenness in the floor will thus twist the case, jamming its doors and drawers.
From Fine Woodworking #32
For the full article, download the PDF below:
Fine Woodworking Recommended Products
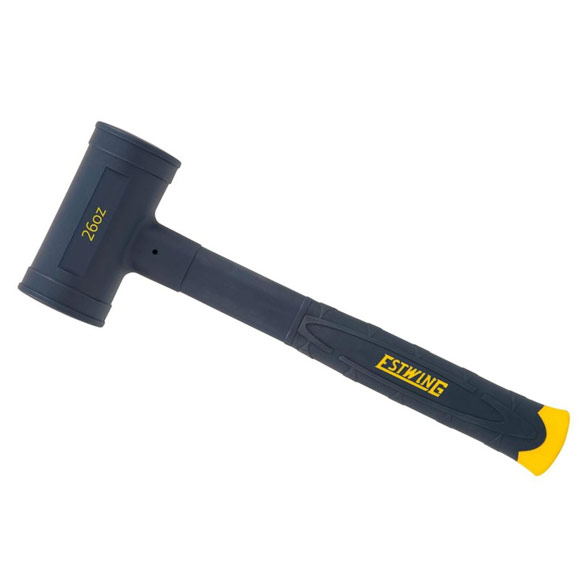
Estwing Dead-Blow Mallet
Bessey EKH Trigger Clamps
WoodRiver Router Bit Storage Case
Log in or create an account to post a comment.
Sign up Log in