Advice on prospective new business?
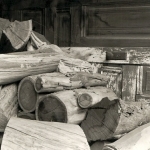
Need some constructive help…
I have a prospective client who give stained glass classes on the weekends. She previously had a “kit” table she would buy from Ikea to be part of one of the projects the students would make. This table was your typical side table or end tabe that would pretty much collect dust for the most part – except for the stained glass picture the student would create on the top. She has since been unable to get the “kits” from Ikea and is looking for me to quote it and make up a proto type.
REMEMBER…. This needs to be a “kit” the average person can assemble in class or at home after the glass top has been applied. So the student may know nothing about building furniture let alone know what kind of wood they are working with. Ease has to be #1 the way I am thinking!
The glass pieces are assembled with water based morter which makes me wonder how she ever got away with a solid wood top before without it cupping and cracking when it dried out – but she has never had it happen …..yet! This was of thinking I was wondering about plywood top with solid wood edging? Might kick myself later for it due to the pain it sometimes is to apply…but anyway.
Attaching the appron to the legs….sliding dovetail joint? Slide them in from the top while the top is not attached, a spot or two of glue to keep them from backing out and the leg falling off when it is moved around…..then either use a button on the bottom to attach the top to the appron (the back side of the appron would be slotted to accept the solid wood button then one screw through the button into underside of the top to hold it on)??
Any suggestions?
Table size currently: 18-1/2″ tall with a 13″ sq top – she is unsure but thinks it might be pine? If from Ikea – I doubt it, but have been wrong before.
will try attaching a picture of the old table (if it will work) notice the appron is down on them from the top – was thinking of making it wider and up near the top?
Replies
The quickest and easiest way to make a "simple" idiot proof kit would be to use festool domino jointery. Also very quick and easy.
Work Safe, Count to 10 when your done for the day !!
Bruce S.
Okay....
One person thinks I am nuts in using sliding dovetails....the other is suggesting a specialty tool that I do not have. Although it would be nice to add to my shop - just not yet.
I am thinking I need a design that will be easy to assemble by the lay person as well as being sturdy. From what I gather this woman charges enough for her classes.....I think if I was paying for the class, I would want a table that could stand up to a few years of what ever would be thrown at it.
If I use traditional mortise and tennon joints, then the person will need to have clamps to assemble the table - does the average person have clamps kicking around - doubt it.
Use typical knock down hardware.....will it be strong enough in solid wood with the movement as the temperatures change?
Hmmmmmm.....might have gotten myself into a pickle here!
If you are competing against this:
http://www.ikea.com/us/en/catalog/products/80104268
you're wasting your time. Of course, that table is particleboard, including the legs! No way can you compete on price with Ikea. Why can't she get any more tables from Ikea - are they too expensive? What is her maximum price? If you had posted your question 6 days earlier I would have taken it as the joke it is. I mean no offense, but this is the ultimate customer from hell - customer walks in with an Ikea catalog under her arm and asks if you can make this (pointing to table in catalog) for less. Ha ha.
I agree with you about the customer from hell.....don't think she has got that far yet. No the table you are showing is not the kind she has had in the past. Think of your typical table you would see at a country store - likely made of pine, square legs, nothing fancy, square top, with an apron around it. The question is....how the hell do I make a table that is stable, reasonably priced, and in a kit with some assembly required by a person who knows very little about assebling joints?
I think my biggest issue is to have a design that is simple but strong once assembled with minimal tools required.
??
I hate to be the one to suggest this. But have you considered pocket hole joinery? For a table of this size it's probably sturdy enough joinery to last for a while.
Although the class members won't have the clamps necessary to hold the parts in place while the screws are driven home, if you pre-assembled the tables to establish the holes in the mating pieces and labeled them, that might do a good enough job of registering the pieces for reassembly.
Pocket holes are very quick to produce, of course, and also have the advantage of being "disassemble-able."
Another idea just occurred to me. If there was a quick way to produce a shallow dado or groove (dado blade in the tablesaw? Router table?) into which the apron could nestle into the leg, that would eliminate the tendency for the apron to shift while the pocket screws are driven.
ZoltonIf you see a possum running around in here, kill it. It's not a pet. - Jackie Moon
>>"....The question is....how the hell do I make a table that is stable, reasonably priced, and in a kit with some assembly required by a person who knows very little about assebling joints?"I'll agree with others -- competing on price against huge factories is like jousting with the wind.But you can try, and you might meet with some success. So, I'll offer some thoughts.....Easy to assemble -- I'm thinking that you need to make up these kits using "knock-down" hardware. Those are the connectors and cams that your competition is using, and that customers will expect. You'll need to cut each piece and shape it, and drill the needed holes, pilot holes, and counterbores.Stable -- to a great extent, this will be a function of your execution. Joints that tighten nicely (using a spot of glue and a cam) will cure up nicely, and stay tight. Stability might also be enhanced by using wood that is inherently stable, as opposed to wood that has a lot of seasonal movement.Reasonably priced -- here's the part that's easy to say, almost impossible to do. Buy wood that is absolutely perfect quality, pre-milled to sizes that you'll need, and pre-sanded. And buy it for less than ten cents a board foot. When you get your first shipment of wood, plan to work for something less than minimum wage doing the production. Oh -- and don't forget about the bookkeeping and accounting tasks, the purchasing and procurement, the packaging and delivery, the customer service and warranty issues..........Good luck. Although there might be some money to be made here, competing with (or even following behind) Ikea is not easy.
Politics is the antithesis of problem solving.
Ooooh SO TRUE!
One thing people might be forgeting....she supposedly has exhausted all her other possibilities? So she is kinda relying on me to provide something for her - kind of a crappy spot to be in. I need to produce something that is fairly resonable for her - I do not want to make it look like I am putting the screws to her on this project. For sure if it works out I want the future business.
I like the idea of using the knock down hardware for ease - I just hate the idea of seeing it on something I built. My wife would agree..... I am a little anal about using much more than wood screws on my furniture I build. It kinda driver her nuts, but I guess I will have to lower my standards?
So if I use the knock down hardware to attach the apron to the legs, how would you suggest attaching the top to the apron? Just counter sink the screws from the bottom of the apron up into top?
Any thoughts on what should be used for the top - plywood with solid lipping? Or stick with a solid wood and hope to have the same success that she has in the past with no wood movement? Yea right!
Mountain,My Hale Rock Maple kitchen table used knock down furniture parts. The legs have the half metal/half wood screw and metal brackets between aprons that the leg gets attached to with a washer and nut.
>>"...how would you suggest attaching the top to the apron? "More knockdown hardware, but you don't need four -- two connections should do here.>>"Any thoughts on what should be used for the top - plywood with solid lipping? ".I'm thinking 1/2" MDF, with a seal coat of something, so that water won't be a problem (like the water in the mortar/grout the glass workers might be using).Or ply......And in either case, you might want to consider edge-banding it.
I'm not liking the idea of solid wood for the tops -- too much movement, especially in the lower-cost woods that you will (eventually) migrate toward. The movement might cause the wood to crack. Worse yet -- it might cause the glasswork to crack.Politics is the antithesis of problem solving.
I am liking the feed back, certainly giving me an idea of some things I have overlooked or just not considered!
Going to shop now, will see what I can come up with for idea's and do a couple test pcs.
Hmmmm...MDF with pre-catilyst lacquer sprayed on it to seal....wonder if that would work for the top? Or would it just sit on top too much and then crack off possibly?
Wouldn't it be easier for you to build the tables, not 'kits'? If the quantity isn't too large, you could deliver 8 ot 10 at a time, and her students could take home a table of this size in the backseat of most cars.
Students would probably appreciate a 'built' table instead of a kit, and you could build a sturdy table that you won't be ashamed to have your name on in 3 or 4 years.
I agree with mms on building a good table, even attatch your name on it for future business. I think the clients will pay more for quality. If you still have to make a knockdown table what about the cam lock joints. Clients just have to lign up the stud with the arrow on the cam and turn the cam with a screw driver. Pretty simple.
Ikea isn't the only company that makes "knock down" furniture, although they do a better job of it than most. Go to Walmart, K Mart, Target, etc, and check out some of their displays to see how their stuff goes together. Most of the pieces are pretty simply made and the assembly hardware is available on the internet. The stuff I've seen usually only requires a screwdriver, allen wrench, and/or a crescent wrench.It won't be heirloom quality, but you should be able to use their methods to make servicable pieces.The real trick will be hitting her price point. After you've figured out how you would make the "kits", and decided on your price, about the only "wiggle room" left would be a volume discount. (The unit cost to make ten at a time is less than making one.)FWIW, when people come to me with an Ikea catalog, I give them the five minute speech about economies of scale and tell them that I can't even start my saw for the Ikea price. - lol
Sliding dovetails... you gotta be dreaming. She's going to be expecting a very inexpensive table kit. You'll be lucky to keep the cost down with screws and dowel buttons. But that's the way I'd go if I were you. And plywood for the top. Maybe talk her into applying glass to the edges, that'll save you some lipping time.
Dowels,
Much of the Ikea furniture is assembled with dowels and knock down hardware.
Assuming that the students are assembling the table in class, your client could provide them with large rubber bands while the glue sets.
Plywood for the top with solid edging.
ASK
Ask her how much she wants to spend.
That will be your answer.
Why waste time designing something that you can't build?
F.
How about this...
Each apron is drilled for two dowel holes with a single pocket hole centering the two dowel holes. Each leg has corresponding dowel holes.
The do-it-yourselfer needs only apply glue to the dowels and drive home one screw per attachment. No clamps needed and the two dowels make everthing self aligning.
In the end the joint is made with two dowels and a screw - definately strong enough.
If there is an extra couple bucks in the budget, you can add a plastic bag with pan head screws, dowels, glue and a low end screw driver. Maybe figure 8s to attach the table top.
These folks are taking a crafty class. I think they will be pretty much able to assemble that.
Something like this:
___ _______________________
| | _ |
| | |
| | |<== Apron
| | _ |
| | |_______________________
| |
| |
Leg
Construction is simple. Make everything up like butt joints, then make up a couple of jigs to align the dowels holes and you can bang them out by the dozens.
Good luck with it...
Oh yeah, and for just $15 more, the student can opt for the fancy version with the tapered leg!
Frank
More good points .... thanks!
Issues I have....I personally....HATE dowel joints. Perhaps it is just me, but any time I have tried to do them, they are always screwed up. I find them a real pain in hind end to say the least.
I liked the idea of knock down hardware - as long as I can make it work. I went to shop earlier tonight, machined some pieces out of pine I had. I made the legs 1-3/4" square x 18" long. Then I made the apron 2-3/4" wide by 1" thick. I have it clamped up on the bench now upside down to see what it might look like.....not too bad? Wouldn't be my choice, but hey I am not the one buying it - I just need to somehow sell it to her! Was looking at Lee Valley catalogue earlier too for the hardware. A bag of 10 pcs cost under $5.00 Canadian. Not too bad I do not think, since I would only use 4 per table. Was looking at the stuff in the clamps and thought if I made the two sides assembled (using a sliding tennon likely the easiest). Glue it up square then the students would only have to attach the 2 aprons with the knock down hardware. If I used 2 per leg of the hardware it might get a little bit crowded? Will not know until I pick up some from Lee Valley and drill some holes and see what will run into what or if everything will be good? I guess that means a trip to the city this weekend.....wonder if I can get away without the wife wanting to go shopping too....hmmmm
Recently I made a corner table for my mom and being that I live over seas it had to be light for portability and easy to assemble as she is all thumbs!
I opted for sliding dovetails as they were fool proof and easy to assemble, and contrary to what some said if your doing a run like forty legs there is nothing simpler. After initial set up there is nothing more monotonous!
Chaim
chaim,Oh sure, now she's all thumbs...maybe the consequence from changing all those diapers. Lovely table :)
yea don't I know it! I got 6 of my own now and I've definitely come to a new level of appreciation.
Chaim
Thank you for the input folks! I appreciate it. I am going to Lee Valley tomorrow to p/u some hardware - going to try the cam lock idea first. I made up the legs and apron the other night, going to see how I make out with the cam locks. If that doesn't work - I think I am going to go with the sliding dovetail idea. Will see what happens next week when I get back to working at it. I have to work this long weekend so no time until Tuesday or Wednesday to get back at it.....hopefully it all works out?
Thanks for the input.....nice pictures of the corner table too.....bet she liked it!
Thanks!
Chaim
This forum post is now archived. Commenting has been disabled